As former CEO of Fannie Mae and Chevy Chase, Maryland-based Berkadia Commercial Mortgage and founding partner and former managing director of BlackRock, Hugh Frater has had a front-row seat for the twists and turns of the U.S. economy and its housing sector for a long time. So, when you ask Frater how the country got to this point — where housing costs have risen dramatically for the average American — his answer is going to go back to the 1970s.
Citing the period from 1972 to 1974, apartment developers delivered 2.2 million units to 24 million rental households, Frater said. From 2020 to 2022, as concerns about oversupply increase, 1 million units are being delivered to 44 million rental households.
“We delivered twice as many units to half as many renting households in the early 70’s as we are now,” Frater told Multifamily Dive. “And not much has changed in homeownership rates — maybe it's a percent higher — and vacancy rates are almost identical. But what has changed is that we have been undersupplied in the market for a long time.”
In what he refers to as his “fourth retirement,” Frater in June became chairman of New York City-based Vessel Technologies, a company that aims to help close the affordability gap by designing and manufacturing what it says is a more cost-efficient building system. Vessel prefabricates key multifamily building components, such as wall and ceiling panels, at a facility in Pennsylvania. It recently received funding from San Francisco-based venture capital firm Mastry Ventures and LENx, the venture arm of Miami-based homebuilder Lennar.
Vessel is seeking franchisees to own, operate and even develop these buildings. But the firm, which has 12 projects in development throughout the Northeast with plans for national expansion, is also prepared to develop and even hold the apartments built with its system if necessary. Here, Frater talks with Multifamily Dive about the slowdown in lending and Vessel’s franchise model and manufacturing process.
This interview has been edited for brevity and clarity.
MULTIFAMILY DIVE: What was the main factor that caused the slowdown in housing production over the last 15 years?
HUGH FRATER: Some of it relates to the 2008 financial crisis. There has always been a very, very clear relationship between housing prices and housing starts with a bit of a lag effect. When prices went up, builders built. When they went down, builders delayed. The relationship completely severed in 2008 and no one has been able to fully explain it.
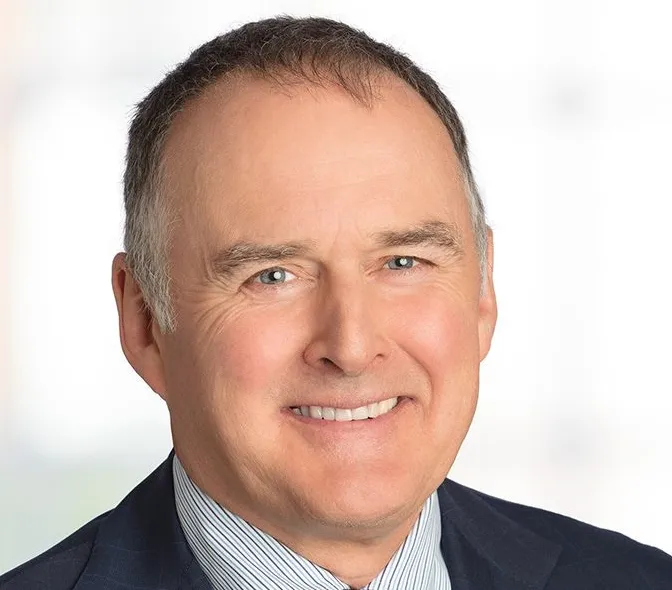
I think it relates to the banks getting so badly burned in land banking for homebuilders and losing so much money on real estate in 2008 that it took them a really long time to get back into the lending business for both residential construction and multifamily construction. A lot of them also lost an enormous amount of money on condo lending.
Vessel aims to streamline the construction of new apartments. How does its franchise concept work?
There will be some franchisees who are experienced developers who will be in a position to acquire the land and entitle the land. And all they will be acquiring from us is the building system, which is the structure and the smart hub that actually controls the tenant features.
In other cases, we will acquire the land, we will entitle the land, we will deliver the system and there may be a third-party equity owner. But there could be a local franchisee.
Do you have an example of that?
In our pilot project in Trenton, New Jersey, our franchisee is a local fire captain. And he knows the neighborhood really well. He handpicked all the tenants. And he receives a fee per unit for managing the building.
He's not required, in his case, to put up the kind of capital that you would need to buy the land and entitle the land. We'll have a mix — just like any other franchise operation — of company-owned stores and third-party-owned stores.
So, Vessel could be the holder of the asset?
We could be. Our project going up in New London, Connecticut, right now is owned by a small fund that we put together. We could be in for 100%. We could be in for 5%.
How does the manufacturing process work?
It's not different from what you see in the single-family business in manufactured housing. We have a factory in York, Pennsylvania, that produces the panel system that is then shipped flat to the site and then assembled on site. On site is the second factory, in effect.
We're producing most of the building offsite, and then it is assembled on site. And that's where you're including the mechanical, electrical and plumbing elements. Some of those are already embedded, and some of them can be put together on site. Then, you’re finishing the interiors on site.
Outside of advances in the manufacturing and delivery of building systems, what else needs to occur to make housing more affordable?
Zoning reform continues to be a huge part of it. There is kind of a revolution going on in zoning reform. There isn’t a single state in the country that hasn't introduced or isn’t talking about zoning reform bills.
Click here to sign up to receive multifamily and apartment news like this article in your inbox every weekday.